Safety Level
Depending on bicycle type a bike‘s handlebar system has to meet a range of safety requirements. An e-bike, for example, has to satisfy very different demands from a conventional touring bike. A mountain bike is subject to much greater strains than a city bike. In each case the basic principle which applies is that requirements always increase with weight – and the overall weight is decisively influenced by the individual body weight of the cyclist!
How can the right handlebar system be reliably identified, and how can consumers be sure that the handlebar system on their bike is safe?
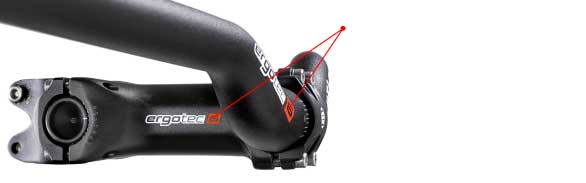
Finding a safe handlebar system has never been so fast. Safety has also never been so easy to identify, because the handlebar system itself now indicates how safe it is and the purpose for which it is suitable.
For all bicycle types.
Each part of an ergotec handlebar system has its own Safety Level. The table enables you to read immediately which bike and specific weight loading the individual system components are suitable for.
The right combination
In the ideal case you should combine handlebar system components with the same Safety Level. However, you can also combine elements with different Safety Levels, but safety will then be at the lowest level which is applied.
Tested as complete systems.
ergotec handlebars and ergotec stems are tested for strength – not individually but as systems! This is the only way to achieve real safety
Testing standards are specified by European norms, but in some areas ergotec has internally even increased the testing requirements. The applicable long-term tests run round the clock at our ergotec safety test centre. No other handlebar manufacturer in Europe has such a comprehensive testing facility.
TEST PROCEDURE
Handlebar safety
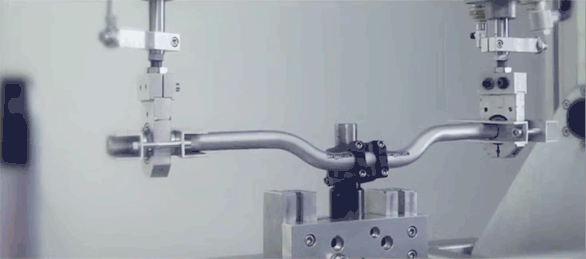
No other bike handlebar manufacturers in Europe have as large a testing centre as we do at ergotec. Furthermore, our products are tested frequently at recognised independent institutions. The test configuration is defined by European standards. 100,000 anti-phase load changes and 100,000 in-phase load changes are applied to the handlebar/stem unit. Requirements: The test subject must not break or show visible cracks. The table shows which test forces (measured in Newtons) are applied to the handlebars and the stem in the tests.
Type of bike | Anti-phase | In-phase |
---|---|---|
Children's bikes | 115 N | 190 N |
City bikes/trekking bikes | 200 N | 250 N |
E-bikes 25 | 240 N | 300 N |
Mountain bikes | 270 N | 450 N |
Racing bikes | 280 N | 400 N |
ergotec Certificate
Tougher testing for e-bikes 25 and everyday bikes experiencing a lot of strain
We apply our own in-house HUMPERTplus standard in order to put handlebar systems of e-bikes 25 and heavily-loaded everyday bikes through their paces. As part of this process, we test with 100,000 load changes and correspondingly higher forces as well as an additional 10,000 load changes in an angle of 25° with even higher values:
HUMPERTplus | Anti-phase | In-phase |
---|---|---|
100,000 load changes at 0° | 250 N | 350 N |
10,000 load changes at 25° | 300 N | 450 N |
Anti-phase testing
In-phase testing
STANDARDS
European standards
Bike handlebars must comply with certain European standards. For our target group, there are four different standards – for children's bikes (DIN EN 14765), for city and trekking bikes (DIN EN 14764), for e-bikes 25 (DIN EN 15194), for mountain bikes (DIN EN 14766) and for racing bikes (DIN EN 14781).
Higher standard
At ergotec, we have defined our own in-house standard, which
- sets much higher standards for the handlebar and stem and
- always examines the combination of handlebar and stem.
ALUMINIUM OR STEEL
It has already been proven time and again with everyday bikes and e-bikes that steel handlebars are a better choice, due to their material properties. In comparison with aluminium, steel is stronger, tougher and longer-lasting. The only disadvantage is that steel handlebars have a greater mass density and therefore weigh more.
This was the challenge that the development of the new micro alloy steel material was intended to address. After a 3-year research period and many tests, we have managed to develop a steel alloy which, despite its decreased material density, is still much tougher. The handlebars made from the new micro-alloyed high-strength fine-grained steel alloy MAS are produced observing the highest quality and environmental standards exclusively in our parent plant in Germany in accordance with DIN EN ISO 9001 and 14001.
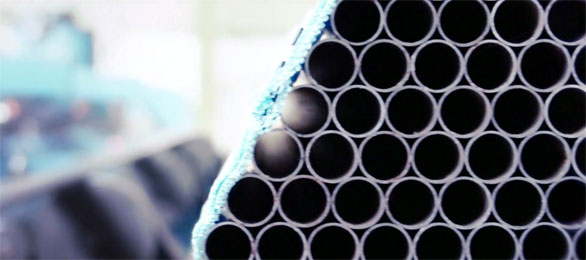
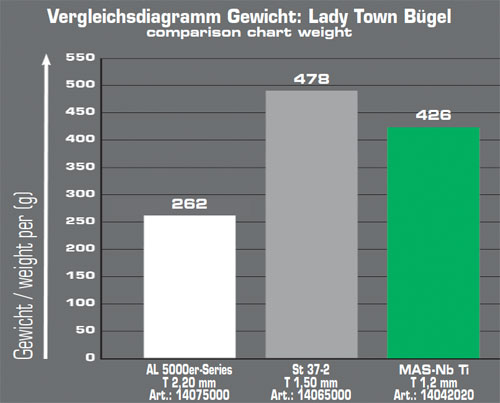
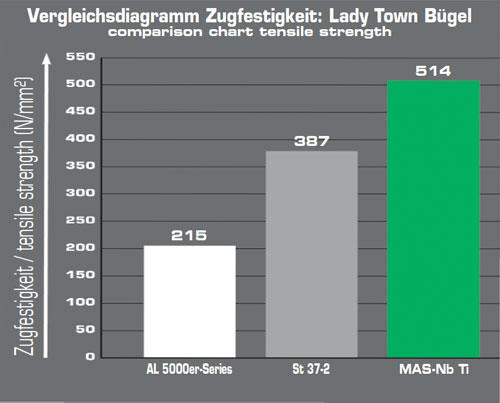
ASSEMBLY
We recommend having parts such as handlebars and stems fitted only by a specialist workshop. Specialist bike retailers know the safety aspects of assembly and are responsible for carrying it out appropriately.
SAFETY INSTRUCTIONS
Do not combine aluminium handlebars with a steel stem. There is a risk of breakage!
When transporting the bike by car, the bike may not be attached upside down on the handlebars, otherwise high dynamic forces shall act on the handlebars, which may lead to early material wear and tear and consequently breakage.
Monitor the torque value of the screws after approx. 500km and then regularly as part of the service period, at least once a year.
When attaching handlebar bags or baskets, you must be careful not to exceed the maximum load of 10kg. Heavier loads can cause the handlebars to break.
If damaged, the handlebars absolutely must be replaced.
Due to material wear and tear, aluminium handlebars must be replaced after 10,000km or three years at the latest.